精密部件制造
产业大脑
首页
行业解决方案
标识服务
供应链金融服务
资讯中心
关于我们
登录
注册
一季度规上工业增加值同比增长6.1%,为8个季度以来最高——工业经济运行平稳向好2024-04-19 10:13:324月18日,国新办就今年一季度工业和信息化发展情况举行新闻发布会。数据显示,一季度规模以上工业增加值同比增长6.1%,较2023年全年提高1.5个百分点。工业和信息化部副部长单忠德在会上介绍,工业经济保持较快增长,高质量发展取得积极成效,总体实现良好开局。 工业企业利润连续增长 工业是国民经济的主体,工业稳则经济稳。一季度规模以上工业增加值同比增长6.1%,为8个季度以来的最高值。 看总体,前两个月,规模以上工业企业实现利润同比增长10.2%,实现了自去年8月份以来的连续增长。一季度工业投资增长达13.4%,规模以上中小企业工业增加值同比增长7.4%,多要素赋能工业经济持续向好。 工业大省大市和重点行业保持稳定增长。31个省份中有28个工业增加值同比增长,江苏、山东、浙江、福建、湖北等9个工业大省增速高于全国平均水平。50个工业大市中,深圳、苏州、合肥、南通、台州、东莞等工业大市实现两位数增长,工业大省、工业大市发挥挑大梁作用。 高技术制造业和新兴产业保持快速增长。一季度,高技术制造业增加值同比增长7.5%,较去年四季度加快2.6个百分点。新兴产业典型产品保持较高增速。太阳能电池增长20.1%;与光伏相关的多晶硅、单晶硅增速高达50%以上;一季度新能源汽车产销同比分别增长28.2%和31.8%。 一季度工信部对3.6万家重点企业调查问卷显示,76%的企业预计其产值二季度将增长或持平。截至2月底,规模以上工业企业户数较上年底增加1.9万户,达到50.1万户。“工业经济回升向好的积极因素持续累积,工业经济发展空间大、信心足、动力强。”单忠德说。 信息通信业优势巩固 近年来,信息通信业技术快速发展,实实在在提升了人民群众的生活品质。一季度,电信业务收入达到4437亿元,同比增长4.5%,总体保持稳步增长。 基础设施快速推进——截至3月底,全国累计建成5G基站达到364.7万个,5G用户普及率超过60%,具备千兆网络服务能力端口达到2456万个,全球首条400G全光省际骨干网链路正式商用,更好地支撑算力和数据要素跨主体、跨类型、跨地域高效互联互通。 关键技术加快突破——目前已完成高中低频段全覆盖5G轻量化商用验证,量子计算原型机研发性能指标不断提升,量子纠错试验验证取得突破。同时,产业实力稳步提升。一季度,中国5G手机出货量达5643万部,占同期手机出货量的83.7%。 数实融合持续推进。目前5G应用已经融入97个国民经济大类中的74个,在工业、矿业、电力、医疗等重点领域规模推广,“5G+工业互联网”项目数超过1万个,应用赋能向核心控制环节加速拓展。个人应用方面,生成式人工智能在聊天机器人、智能搜索、文本生成等应用中推广普及。一季度,移动互联网流量同比增长14.3%。 工信部新闻发言人、总工程师赵志国表示,将进一步巩固提升信息通信业竞争优势和领先地位;加快落实大规模设备更新相关政策,推动信息基础设施优化升级;推进算力基础设施协同发展,加快形成全国一体化算力体系;推动5G与大数据、云计算、人工智能等多种技术融合,加快5G演进。 新型工业化加快推进 当前,各地区各部门大力推进新型工业化,制造业持续向高端化、智能化、绿色化发展。 高端化发展取得新突破。今年以来,统筹实施关键核心技术攻关工程、产业基础再造工程和重大技术装备攻关工程,创新成果不断涌现,比如,300兆瓦级F级重型燃气轮机首台样机总装下线,立下重型燃气轮机自主创新发展历程中的重要里程碑。扎实推进制造业重点产业链高质量发展行动,发展壮大先进制造业集群。 智能化水平取得新提升。数字技术与制造技术,数字经济与实体经济,信息化与工业化,人工智能与制造业等深度融合加快推进,目前已培育421家国家级智能制造示范工厂。央地协同出台系列政策支持企业数字化转型、智能化改造,全国已建成近万家数字化车间和智能工厂,智能制造装备产业规模已经达到3.2万亿元以上。 绿色化发展取得新成效。产业结构方面,先进制造业比重持续提升,绿色装备和产品供给进一步增强。一季度,新能源汽车市场占有率超过31%。产业布局方面,工业领域氢能、新型储能等应用场景不断拓展,首个万吨级绿氢产业化示范项目已经建成投产,钢铁行业首套百万吨级氢基竖炉已经点火运行。钢铁、有色金属等传统行业规模以上工业单位增加值能耗继续下降。 单忠德表示,未来将继续推动制造业高端化、智能化、绿色化发展,不断巩固工业经济回升向好态势,培育发展新动能,为工业经济高质量可持续发展提供有力支撑。(记者 李婕)
有色金属铸件行业:市场动态、发展趋势与前瞻2024-04-18 10:56:19有色金属铸件是现代工业中不可或缺的一部分,其市场动态和发展方向一直是业界关注的焦点。全球经济的稳步增长和科技的快速进步为有色金属铸件行业带来了前所未有的发展机遇。 在市场需求方面,有色金属铸件在多个重要领域均显示出强劲的增长势头。特别是在汽车制造业,随着新能源汽车市场的不断扩展和智能化技术的深入应用,对铝合金压铸工艺的需求持续上升。此外,航空航天、电子信息、机械设备和能源化工等高端装备领域,对高性能和高精度的有色金属铸件的需求也在增加,为行业的扩展提供了广阔的空间。例如,2023年10月26日,力劲集团发布了迄今为止全球最大的压铸机——16000T超大型压铸单元,这一事件标志着中国压铸技术的重大突破。 从发展趋势的角度来看,有色金属铸件行业正向智能化、绿色化和高端化方向发展。随着工业4.0的推进和智能制造技术的广泛应用,如一体化压铸技术在汽车制造领域的运用,通过高压压铸技术将多个单独、分散的零部件高度集成,一次压铸成型,不仅提高了生产效率,还显著降低了成本,并改善了产品质量。同时,增强的环保意识和对可持续发展的追求促使行业更加注重绿色生产,采用环保材料和节能技术,减少生产过程对环境的影响。 尽管有色金属铸件行业的发展前景光明,但也面临诸多挑战,如原材料价格波动、贸易保护主义抬头和技术快速更迭等,这些都可能对行业的持续发展造成不确定性。因此,企业需要紧跟市场和技术发展趋势,加强创新和市场开拓,提升自身的核心竞争力和抗风险能力。 综上所述,有色金属铸件行业在全球经济增长和科技革新的双重推动下,预计将继续保持强劲的增长势头。行业企业需抓住机遇,应对挑战,确保可持续发展。
常州“三个持续”提升新能源汽车产业竞争力2024-04-18 10:29:35近年来,常州持续发力新能源汽车及汽车核心零部件产业,在近日发布上市的小米SU7车型中,电池、传感器、高压连接器等核心零部件均来自该市企业。 (一)产业链条持续延伸。全市目前产品门类齐全,围绕动力电池、电机电控、车身、底盘等领域形成较为完善的产业链。其中,动力电池产业集聚企业160余家,并在全球动力电池装机量TOP10中占据3个,产业链完整度居全国首位;新北区新能源汽车电气设备产业集群入选2023年度国家级中小企业特色产业集群。 (二)龙头企业持续发力。加快行业龙头企业招大引强,推动形成“龙头企业+配套产业”的产业集群。江苏时代成为全市首家、全球锂电行业第三家“灯塔工厂”;理想、比亚迪带动全市2023年新能源汽车产量达67.8万辆,同比增长97.3%;中创新航、星宇车灯分列2023中国汽车零部件企业百强榜22、50位。 (三)企业服务持续完善。深入实施企业股改上市“龙腾行动”,到2025年,力争新能源汽车零部件产业60家企业完成股改。持续发力新能源汽车检测认证领域的生态构建,大力推进全场景智能网联测试基地建设,当前已集聚新能源汽车检测中心等公共服务平台10多家。
2024年有色金属质量会议预安排(按时间)2024-04-08 15:49:192024年有色金属质量会议预安排(参附件)
2024国际氢能与燃料电池汽车大会暨展览会(FCVC 2024)2024-04-08 15:42:54大会介绍 在碳达峰碳中和背景下,中国正在积极推动可再生能源大规模开发利用和石油化工钢铁等行业的绿色转型,其中氢能的利用是多个行业降碳转型之路的有效手段,作为氢能在交通领域的重要应用场景,氢燃料电池汽车是全球汽车动力系统电动化转型升级的重要方向,各行业正在积极推动可再生能源制氢、氢储能等应用,并协同氢燃料电池汽车打造氢能应用闭环。 2024国际氢能与燃料电池汽车大会暨展览会(FCVC 2024)将于6月4-6日在上海汽车会展中心召开。本次大会将以 “聚力创新 氢动未来—坚定推动氢能与燃料电池汽车高质量发展” 主题,共设“1场全体大会、5场行业边会、7场主题峰会”,同期还包括3天专业技术和设备展览,涵盖技术参观、新品发布等在内的多场精彩活动。大会将为行业搭建权威专业的国际合作交流平台,共同推动氢能与燃料电池汽车技术融合发展,实现产业共赢。
压铸早报2024/4/8星期一2024-04-08 15:08:53奔达模具启动IPO项目 日前(3月25日),佛山市南海奔达模具有限公司(简称:奔达模具)召开IPO项目启动会。此举标志着奔达模具的上市进程取得了新的进展,成为奔达模具快速发展的新起点。 奔达模具,创立于1990年,是一家专业从事铝合金材料性能、产品设计、设备配套、熔铸工艺、模具技术研究和服务的高新技术企业。同时,该公司也具备高压、低压铸造工艺的研究、设计和验证能力。2022年5月,南控集团收购了奔达模具69.2648%的股权,从而成为其控股股东。 拓普、文灿、立中重庆项目建设进展 据重庆沙坪坝发布的消息,目前,沙坪坝区青凤科创城各重点项目正在有序推进中。其中,拓普新能源汽车轻量化底盘系统暨内饰隔音件系统生产基地的内饰隔音件系统模块已经投产,压铸车间的设备基础已经完成,部分设备安装正在进行中,预计5月份完成安装,轻量化底盘系统模块产品预计今年下半年投产。 立中集团年产10万吨高性能铝合金新材料项目已经完成挡墙建设和桩基础施工,正在进行地梁和设备基础施工,预计今年6月主体工程完工。该项目占地约63亩,目标是打造成为新能源汽车及一体化压铸用免热处理铝合金材料、高性能铝合金新材料等产品的研发和智能化生产工厂。 文灿新能源汽车轻量化零部件重庆生产基地项目场平已完成80%,强夯完成10%,预计今年10月完工。该项目占地约128亩,旨在打造集压铸车间、机加车间、后处理及装配等配套工艺为一体的智慧工厂,主要生产中高端新能源汽车的轻量化一体车身结构件、动力系统零部件等关键产品。 贵州宏凯抢抓生产赶订单 据贵州时政凯里报道,在贵州宏凯制造有限公司的压铸生产车间里,工人们正在有条不紊地进行铝合金熔炼、高压铸造、清理打磨、抛丸、机械加工和检测等各项工作。由于订单充足,公司正在全力以赴赶制订单。 贵州宏凯制造有限公司董事长严华介绍,公司主要生产汽车铝合金压铸零部件,目前的主打产品有十五六种零部件,年产量超过500万件。为了适应市场需求,公司正在建设二期工程,计划新增一批设备和8000平方米的厂房。今年投产后,预计产值将达到8500万元以上。 亚通精工拟在常熟投资一体化压铸项目 近日,烟台亚通精工机械股份有限公司(简称“亚通精工”)发布公告称,其全资子公司江苏弗泽瑞金属科技有限公司(简称“江苏弗泽瑞”)计划与常熟经济技术开发区管理委员会签署《项目协议书》,在常熟经济技术开发区投资建设高性能铝合金材料及汽车轻量化零部件生产项目。 据悉,该项目总投资预计不超过3.5亿元,占地面积35亩,总建筑面积将达到16932平方米。项目计划新增一系列先进设备,包括压铸岛设备、压铸后处理及修模设备、实验室检测设备等以及机加工加工中心和辅助设备。主要产品将包括一体式压铸车身结构件、集成传统车身钣金件、铝合金压铸产品以及门锁支架锻件产品等。项目建成投产后预计将可生产204万套的铝合金压铸产品和200万件的门锁支架锻件产品。 国轩高科入股造车 近日,奇瑞控股集团发生工商变更,新增股东合肥国轩高科动力能源有限公司(简称“合肥国轩”),持股比例为1.95%。合肥国轩为国轩高科的全资子公司,此前已间接持有奇瑞控股集团0.82%的股权。此次增持后,合肥国轩合计持有奇瑞控股集团2.77%的股权。国轩高科也成为继宁德时代后第二家入股奇瑞的电池企业。 国轩高科与奇瑞汽车早在2012年就已建立合作关系,共同探索新能源产品的应用。今年1月7日双方还签署了战略合作协议,拟在乘用车及商用车领域展开全方位合作共同开拓新能源汽车市场。 多家新能源车企发布3月销量数据 近日国内多家新能源汽车企业发布了3月销量数据。其中问界全系交付新车约3.17万辆环比增长50%;理想汽车交付2.9万辆新车同比增长39.2%;零跑汽车交付1.46万辆新车同比增长136%;蔚来汽车交付1.19万辆新车同比增长14.3%;小鹏汽车交付9026辆新车同比增长29%。此外比亚迪汽车销售302459辆汽车同比增长46%;广汽埃安全球销量超3.2万辆环比增长95.1%;极氪交付13012辆同比增长95%。
改善下缸体压铸件缩孔的模具优化设计2024-04-08 15:06:32原标题:改善下缸体压铸件缩孔缺陷的模具优化设计 摘要:介绍了一款铝合金下缸体压铸件的结构特点及缺陷形式,运用“鱼骨图”对下缸体局部缩孔缺陷进行分析。采用局部挤压技术对铸件局部厚大处进行增压补缩,同时加大缺陷部位的型腔冷却,采用“分水盘”结构改变冷却水道进出口位置,避免与挤压油缸的干涉。通过以上措施有效地提高了下缸体的内部和外观质量,大幅提高产品的合格率。 随着汽车轻量化和节能减排的需要,汽车发动机的核心零件缸体和下缸体也逐渐开始采用铝合金代替铸铁材料,通过高压铸造实现产品的大批量生产。但在产品的结构设计上,因功能需要常常会出现局部壁厚厚大区域,在压铸过程中由于铸件壁厚不均匀,厚壁处凝固收缩时间差异大,容易发生缩孔、缩松缺陷,导致泄漏。 本课题研究的下缸体外轮廓尺寸415 mm×325 mm×112 mm,质量6.1 kg。材料为铝合金ADC12,执行标准为:JIS H 5302—2006。ADC12是一种铝硅合金,因其具有良好的流动性、抗热裂性以及很好的气密性,是压铸缸体、缸盖常采用的材料。铸件密封性能要求整个腔体在19.6 kPa压力下泄漏量小于15 cm³ /min,高压油道在343.2 kPa压力下泄漏量小于3 cm³ /min。 1、下缸体压铸件结构特点及缺陷形式 缸体是汽车发动机的主要组成部件,通过缸体将发动机曲轴连杆机构及供油、润滑、冷却等机构联结成为一个整体,其质量直接影响发动机的性能。下缸体是两体式缸体的下部零件,其产品结构及形状如图1所示,由于下缸体的功用决定了其铸件结构的复杂性,上面与上缸体连接,下面安装油底壳,在安装油底壳平面的一侧设计机油滤清器安装孔,同时实现机油滤清器支架的功能。下缸体的整体结构呈箱形,壁厚不均,主要壁厚3.5 mm,中间有五处宽度20~22 mm安装曲轴的横梁,侧向安装机油滤清器孔区域,壁厚不均,内部布置高压油道。铸件的整体结构呈区域分布,中间镂空部位多,同时壁厚严重不均匀导致压铸件的开发难度较大。 图1 下缸体形状及缺陷位置 在新产品试制过程中,铸件加工后进行密封测试,发现在下缸体侧面安装机油滤清器处的高压油道在343.2 kPa压力下泄漏率高达30%,高压油道的形状及尺寸如图1c所示,机油滤清器安装螺纹孔M20 mm×1.5 mm及螺纹底孔为加工孔,侧向Φ15 mm孔位非加工孔。对泄漏零件缺陷部位进行剖切检查,发现在机油滤清器安装孔区域有不同程度的缩孔和缩松,最大缩孔5 mm×2 mm;观察缺陷部位外观,发现在M20 mm孔与Φ54 mm尺寸中间的异形区域,外表面有不同程度的粘料,由此判断高压油道泄漏的原因是铸件局部有严重的缩孔,加工后缩孔与油道孔贯穿,同时由于铸件表面粘料而将表层致密层破坏,从而导致高压油道泄漏。 2、机油滤清器安装孔处缩孔成因分析 2.1 缩孔产生原因 铸件在凝固过程中,由于合金的液态收缩和凝固收缩,往往在铸件最后凝固的部位出现孔洞成为缩孔,缩孔的形状不规则,表面不光滑,色泽偏暗,大小不一,有独立存在的缩孔,也有多个细小而分散的小缩孔。针对铝合金压铸件缩孔缺陷产生的原因,从压铸合金、压铸模具、压铸机、压铸工艺、压铸件结构等方面,利用鱼骨图进行缺陷原因分析,如图2所示。 图2 缩孔缺陷鱼骨图 2.2 下缸体缩孔成因分析 根据上述缩孔缺陷产生的鱼骨图,利用UG设计软件、AnyCasting数值模拟分析软件对产品结构及模具设计进行分析,借助压铸机实时控制系统及红外线成像仪对制造过程进行分析,经过逐项分析和排查,最终确定下缸体机油滤清器安装孔区域的缩孔产生原因如下。 2.2.1 铸件局部壁厚过厚 下缸体机油滤清器安装孔处剖面形状如图1c所示,高压油道周边铸件壁厚8~22 mm,而铸件主要壁厚3.5 mm,此区域壁厚尺寸过大而且壁厚不均,压铸成形后金属液在凝固过程中体积缩小,同时此区域属于填充末端,远离内浇道,无法实现较好的增压补缩,因此出现缩孔缺陷。 使用AnyCasting软件对下缸体凝固过程进行数值模拟,结果如图3a所示,铸件在图示区域出现孤立液相区,孤立液相区最终形成缩孔的概率很大,基于残留熔体模数法对缩孔概率分析的结果见图3b、c。铸件的其他部位承受压力下,分散的缩孔对铸件影响较小,而机油滤清器安装孔处有高压油道,内部的缩孔直接影响铸件的密封性。数值模拟结果与上述理论分析相符。 图3 凝固数值模拟 2.2.2 模具局部温度过高 观察铸件缺陷部位外观,发现在M20 mm孔与Φ54 mm尺寸中间的异形区域,外表面有不同程度的粘料,局部粘料的产生是模具温度过高的一种体现。使用红外线成像仪对模具温度进行监测,结果如图4所示,从中发现机油滤清器安装孔区域模具温度明显高于其他成形表面。由于下缸体的零件结构决定模具上分布大量的预铸孔型芯,这将影响模具的冷却水道的布置。同时铸件缺陷部位在动模镶块中属于局部凸起,压铸过程中被大量金属液包裹,铸件在凝固过程中大量热量无法通过模具快速散出,导致模具局部温度过高,这也是缩孔和粘料产生的原因。 图4 模具温度 3、解决铸件缩孔的模具优化设计 根据上述原因分析,针对压铸模采取以下两种措施解决机油滤清器安装孔区域的缩孔:①在不改变产品结构形状的基础上,将机油滤清器安装孔M20 mm由原来预铸孔型芯变更为局部挤压,在型腔内金属液冷却至液相线和固相线共存时通过液压缸对铸件局部进行增压补缩,以减少孤立液相区缩孔的产生;②加大模具在机油滤清器安装孔区域的冷却,采用分水盘结构改变局部冷却水的进出口位置,从而解决局部冷却不良导致的模具温度过高而产生铸件缩孔。模具的具体优化设计方案见图5。 图5 模具优化设计 3.1 采用局部挤压机构对铸件局部补缩 局部挤压是在模具内直接安装油缸,对产生缩孔的部位直接进行加压,抑制缩孔,以获得高质量的压铸件。下缸体局部挤压结构如图6所示,挤压套固定在动模镶块中,挤压缸固定在动模套板后端,挤压杆通过油缸联结头连接在油缸活塞杆上。挤压时油缸无杆腔进油活塞杆带动挤压杆向前运动,挤压型腔内金属液并直接形成铸件底孔。 局部挤压机构设计的关键是挤压体积,挤压体积过小,即挤入的金属液不足,无法达到补缩的作用;若挤压体积过大,则需要设计大直径的挤压缸,不仅造成浪费,而且在模具有限的空间内无法安装。挤压体积即为需要补缩的金属液体积,其大小取决于铸件局部成形体积,依据经验铝合金局部挤压的补缩体积比通常取5%~10%(预留补缩体积/铸件成形局部的体积)。经计算下缸体机油滤清器安装孔处局部体积约34 cm³ ,设计预留补缩体积V=34×7%=2.38 cm³。依据铸件结构,设计挤压杆直径d=16 mm,挤压杆结构图见图6a,依据挤压体积计算挤压行程L如下: 将上述数据代入式(1)得到L=12 mm。为使挤压时金属流动性更好、挤压影响范围更大,将挤压销前端设计成长度6 mm斜度20°的锥面,挤压初始位置挤压杆伸入型腔10 mm,挤压结束位置挤压杆伸入型腔22 mm,处于被挤压部分的中部,如图6b所示,这样可以使挤压范围更大,挤压补缩效果更好。 根据帕斯卡原理,在已知挤压杆直径和挤压压力的条件下,可以计算出挤压油缸的直径: 图6 局部挤压机构 式中:P挤 为挤压压力,一般取铸造压力的3倍以上,在下缸体中取400 MPa,F挤 为挤压杆面积(m㎡),P缸为压铸件系统压力16 MPa,F缸 为挤压油缸无杆腔面积(m㎡),d为挤压杆直径,D为挤压油缸直径。代入上式经计算挤压油缸直径D=80 mm。设计时考虑安全系数,最终挤压油缸直径取1.25D=100 mm。 3.2 采用分水盘结构加大局部冷却 压铸模具温度是影响压铸件质量的重要因素之一,为保证在连续生产过程中模具温度保持在合理的工作温度范围,常常采用水冷却的方式,对模具型腔进行冷却。通过在模具型腔内设置冷却水通道,通过冷却水循环带走模具内压铸合金产生的大量热量,使用成本低,效率高。冷却水道设计时要求布置在型腔内模具温度最高、热量比较集中区域,下缸体动模型腔M20 mm机油滤清器安装孔区域正是热量集中的区域,模具局部形状如图7a所示。由于M20 mm孔周边布置大量的型芯孔和推杆孔,无法设置横向循环的串联式冷却水道,因此型腔冷却采用垂直方向的喷管式独立冷却。参照图4模具温度图片,对应高温区域增加10处喷管,如图7b所示位置,对局部高温处进行冷却。根据动模型腔局部形状确定水道孔直径10 mm,深度距离前端成形处8 mm,喷管采用外径6 mm,内径4 mm的铜管。由于新增10处小喷管背面有挤压油缸,小喷管后端的进出水无法引出,无法实现单点独立的喷管冷却。为解决局部冷却水进出的问题,增加“分水盘”结构,如图7c所示,在分水盘加工出双层水道,将铜喷管固定在分水盘上,实现喷管a1-4的串联水通道和b1-6的串联水通道。在后端挤压缸不干涉的位置,加工出a组和b组的冷却水进出孔位置。 图7 分水盘结构的冷却水道设计 4、优化设计的验证 下缸体模具经过局部优化设计后,进行批量生产验证,铸件毛坯在机油滤清器安装孔区域的缩孔缺陷得到明显改善,产品经X光无损探伤和剖切断面检查,无明显的缩孔缺陷,优化后的铸件内部质量如图8所示。优化后的模具温度得到有效控制,开模后动模型腔热量集中部位温度控制在180~240 ℃,满足铝合金压铸的工作温度,铸件外观无明显粘料现象。由于铸件内外部质量得到有效提升,产品加工后进行密封测试,安装机油滤清器处的高压油道泄漏率由30%降低到2%以下。 图8 优化后的M20 mm孔区域内部质量 5、结论 (1)“鱼骨图”质量工具是对铸件缩孔缺陷进行分析的有效手段。 (2)采用局部挤压技术能够有效解决铝合金压铸件因局部壁厚过大而产生缩孔和缩松缺陷及高压油道泄漏问题。 (3)对铸件局部厚大、热量集中处需布置足够的冷却水道,利用分水盘结构可以改变冷却水道的进出口位置,避免与模具内其他结构发生干涉。 作者 侯丽彬 李晶 董淑婧 大连科技学院 本文来自:铸造杂志
共 7 条
- 1
页
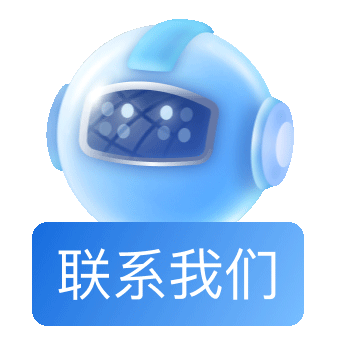